No. 2.3.5
Coating Removal, Grinding/Scraping Method
OUTLINE
This coating removal method uses various grinding and scraping tools, depending
on the composition of the coating material. A knife or dental style scraper is
normally used when a scraping method is desired. A hand held drill is normally
used when a grinding technique is desired. A wide variety of rotary abrasive
materials including ball mills may be required.
To determine the appropriate coating removal procedure the coating must first
be identified. Refer to procedure number 2.3.1.
CAUTION
Abrasion operations can generate electrostatic charges.
TOOLS & MATERIALS
Ball Mills
Brushes
Cleaner
Micro-Drill System
Microscope
Knife
Rubberized Abrasives
Scraper
Wipes
Wood Sticks
PROCEDURE SCRAPING
- Clean the area.
- Remove the damaged or unwanted coating or solder mask using a knife or scraper. Hold the blade perpendicular to the coating and scrape from
side to side until the desired material is removed. (See Figure 1).
- Remove all loose material and clean the area.
PROCEDURE - GRINDING
- Clean the area.
- Insert an abrasive tip into the hand held drill. Abrade away the damaged or
unwanted coating. Move the tool from side to side to prevent damage to the circuit
board surface. (See Figure 2).
- Remove all loose material and clean the area
NOTE
Rubberized abrasives of the proper grade and grit are ideally suited for
removing thin hard coatings from flat surfaces but not for soft coatings since
these would cause the abrasive to "load up" with coating material and
become ineffective.
Rotary brushes are better suited than rubberized abrasives on contoured or
irregular surfaces, such as soldered connections, etc., since the bristles will
conform to surface irregularities while removing hard or soft coatings. (See
Figure 3).
NOTE
The procedure for removing thick coatings is primarily to reduce their thickness
to a thin coating and then to remove the remaining thin coating by the scraping
method.
EVALUATION
- Visual examination or UV light may be used to verify complete removal of
coating.
|
| |
Solutions Across the Board
TM
|
|
|
Product Class: R/F/W/C
Skill Level: Expert
Conformance Level: High
Revision: E
Revision Date: Jul 7, 2000
Repair Service Charge
Coating Removal Required At Outlined Area
Figure 1: Scrape away damaged or unwanted coating with a knife or
scraper.
Figure 2: Rubberized abrasives are best used to remove thin, hard coatings.
Figure 3: Rotary brushes are best used to remove soft coatings.
Figure 4: Removal complete.
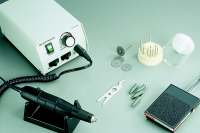
Figure 5: Micro-Drill
System.
|
Tricks of the Trade
This procedure for coating removal is generally the method of
choice for confined areas. You can't beat having a dental quality Micro-Drill fitted with Carbide
Ball Mills for control and accuracy
|
|
|